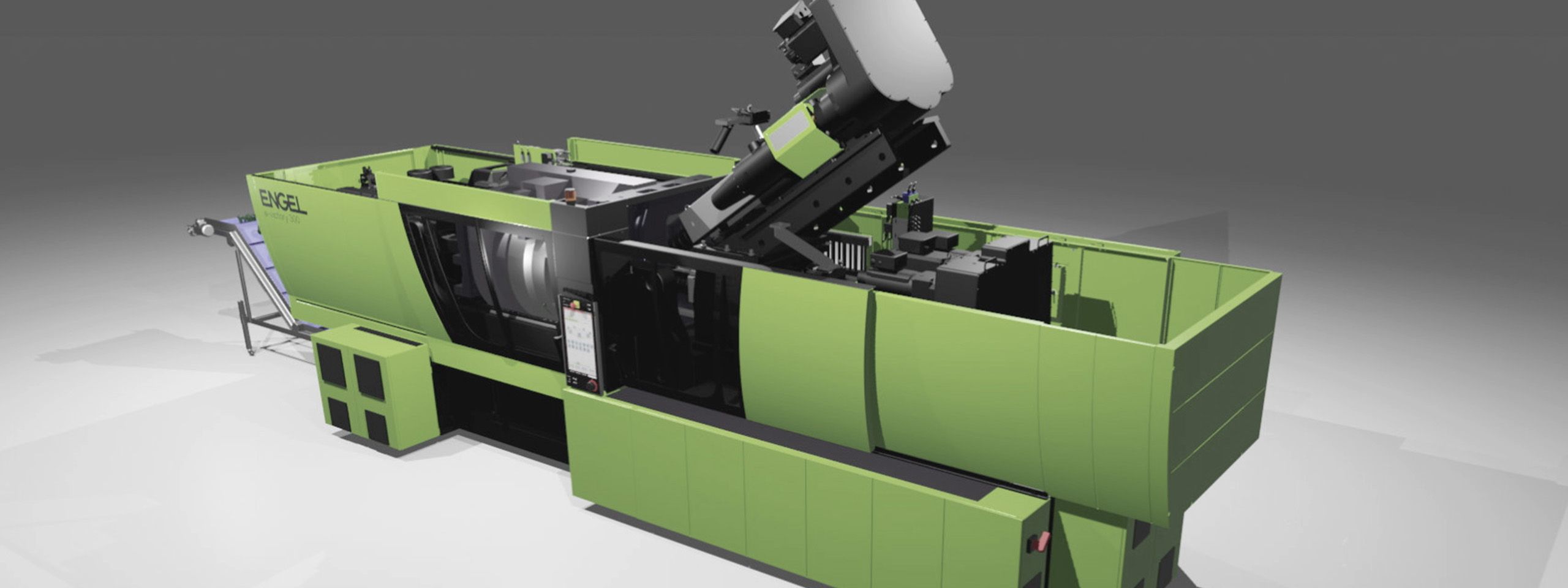
EXJECTION Moulding
1 technology, 2 processes and endless opportunities ...
+ linear process
+ rotating process
Economical, sustainable but above all endlessly innovative.
-
More length for a lower price
The linear EXJECTION technology, characterized by a moving tool slide in the mould and by the use of small injection moulding machines for components with a length of up to 3 m, enables not only the production of functionalized ledges but also the back injection moulding of sensitive substrates, as required for IMD (In-Mould Decoration) and ISS (Integrated Smart Surfaces) technology.
-
Continuous processing
On the basis of the EXJECTION endless technology, Continuous Moulding can also be used to produce injection moulded parts in high volumes with rotary moulds. The integration of upstream and downstream process steps leads to no loss of productivity, which is about 40 % higher compared to injection moulding with multiple moulds.
The continuous injection moulding process can also be used to produce endless profiles with functional geometries such as cross ribs, snap hooks, screw bosses and wall thickness jumps. Such profiles cannot be produced in the classic extrusion process without uneconomical post-processing.
Heading to the future together.
HTP High Tech Plastics GmbH has implemented the EXJECTION technology in Fohnsdorf. Together with IB STEINER, components are developed and manufactured for interested parties with a high level of competence, using all the advantages of the EXJECTION technology to the benefit of our and your customers.