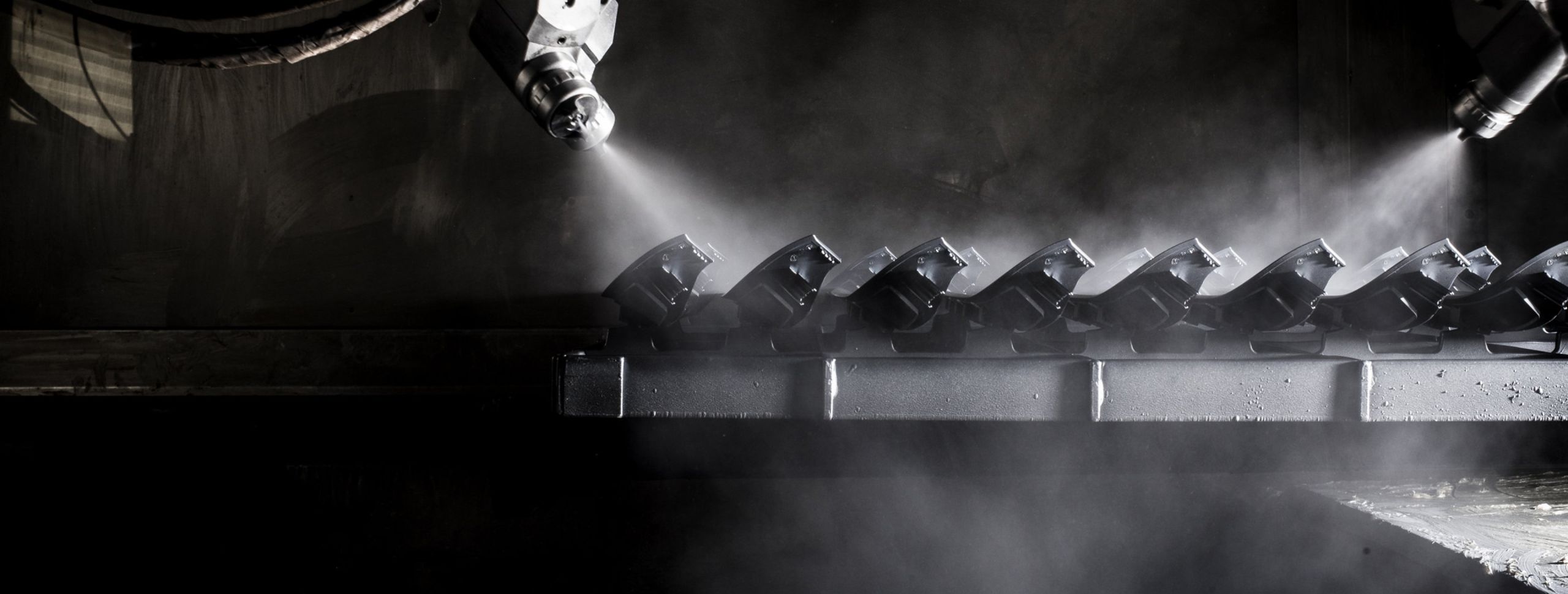
Automatic Painting
* Standard stands for Decor-, Haptic-, Effect- and Laser Varnish supported
- Robotic
- Cleaning:
Powerwash - Aktivation
optional - Painting Method:
2x6 Robotic - Lacquer Layers:
2 layers - Coating System:
solvent- / water-based - Paint Supply:
2K-fully-auto - Surface:
Standard
- Flatbed
- Cleaning:
CO2 Ionisation - Aktivation:
oxidative - Painting Method:
linear on 8 nozzles - Lacquer Layers:
n-layers - Coating System:
solvent- / water-based, UV-hardened - Paint Supply:
2K-fully-auto - Cleaning:
+ High Gloss and Chrome Varnish
Two Combinded Intention - Perfectly Painted Molding Parts.
-
Robotic Painting
On a fully automated painting robot system, we manufacture high-quality painting components for vehicle interior applications via an upstream power washing and ionizing system as well as 2 paint robots with wet separation. In compliance with all environmental requirements, water-soluble two-component PUR coating systems and solvent-based paints from different manufacturers are processed. The system design allows different process sequences such as priming, 2-coat painting or pretreatments by means of surface activation. A closed conveyor system transports the total of 100 rotatable skids after painting over an evaporation, drying and cooling section for quality control and packaging of the finished parts.
Air-Conditioning but no UV-Curing
-
Flatbed Painting
The fully automatic painting system is specially optimized for high-gloss components. For this purpose, the components are cleaned on the paint skids and pretreated with a CO² ionization. In two spray booths with 8 nozzles each, the parts are painted optimally. Both, solvent-containing and water-soluble 2K paint systems can be used for this. The lacquered parts are dried in the directly following fully automated drying magazines. A subsequent optional UV curing offers additional scratch resistance of the finished painted surface.
A 100% quality control with correspondingly careful packaging is a matter of course for our customers.Air-Conditioning and UV-Curing